top of page

SFT vs TCA
Obviously, it has been a very attractive idea to model the roll test in computer environment by skipping the necessity to have a very expensive and time -consuming cutting and testing equipment. But it had its own challenging issues:
_____________________
It requires the computer models for each type of gear cutting equipment and methods of cutting to develop the working surfaces;
______________________
Models developed for each member should be brought together and be rolled like in real conditions;
______________________
Computer system should be capable to handle the amount of computation to get results in a reasonable time.
This idea originally developed by Gleason Works, Rochester, NY about 60 years ago has been a very innovative and efficient tool in design, evaluation and production of spiral bevel and hypoid gears.
​
It became known, and it has this “trade name” up to now, as TCA: Tooth Contact Analysis.
Modeling of gear cutting process and methods based on different equipment and simulation of that with a very accurate visual depiction using so-called TCA (Tooth Contact Analysis) package developed by GEI Systems has become a signature product of GEI Systems in the gear technology area.
​
First versions of TCA would represent so-called unloaded or unstressed conditions during the rolling test. Later, when knowledge of FEA has become more common, this model has been redeveloped in to a LTCA: Loaded TCA.
Even in spite of the fact that models would have some issues to” depict” a true surface, true loads, true stiffness of the housing where this gearset to be mounted, it had a great success in gear industry.
Based on analytical representation of the working surfaces for gear and pinion and the estimated mounting conditions this method is capable of prediction the amount of transmission error and showing the contact between two surfaces during such a virtual roll test.

With a progress in computer industry this analytical (off-line) method of gear’s evaluation has become a complimentary (not competing) product to already existing “real” roll test called Single Flank Test (SFT).
Based on analytical representation of the working surfaces for gear and pinion and the estimated mounting conditions this method is capable of prediction the amount of transmission error and showing the contact between two surfaces during such a virtual roll test.
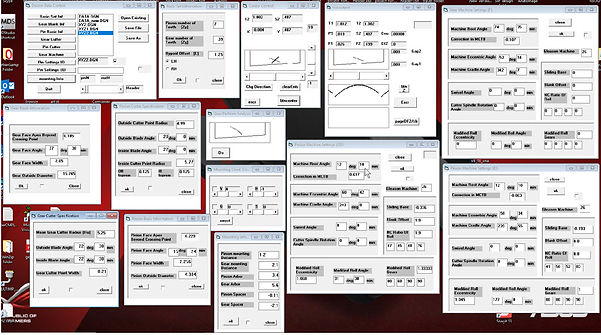
Results obtained from TCA developed at GEI Systems using Visual Studio IDE with VB and Fortran Compilers. This package allows to interactively select the machine type, cutting tools, machine settings and mounting conditions. TE is displayed
Computer - Controlled Single Flank Testing: From Retrofit Option to Advance Design
5000 W 35th STREET • MINNEAPOLIS, MN 55416 USA • P 1.612.922.7816 • F 1.612.920.7955 • W INFO@GEISYSTEM.COM
bottom of page