About SFT
GT40 SFT
Computer - Controlled Articulated Gear Performance Expert System (AGPES)
Based on 7 patents GEI Systems, Inc has developed and built its first fully computerized smartSFT in 1986.
For the next 10- 15 years industry could not accept the TE method as an industry standard until two major gear tool manufacturers: Gleason and Oerlikon have started the production of theirs SFT testers based on TE methods.
An advanced version of a Single Flank Tester GT40 has been targeted mainly for R&D applications with some limited use for production purpose.
​
The tester is designed with one “stationary” spindle attached to the main mounting frame and the second spindle mounted on a 6DOF articulation system.
By introducing GT40, GEl Systems has provided Automotive Industry with a multiple degree of freedom system capable of precise manipulation of a gear surface relative to the pinion surface while under computer control.
AGPES is designed to simulate real environmental conditions such as bearing, shafts, and gear housing spatial stiffness. These environmental conditions would be simulated through the actuator system and computer models of both Tooth Contact Development (TCD) and deflections due to load profiles.
​

A few different configurations for the suspension system, supported by GEI Systems patents, can be offered:
-GT41configured as a 6DOF Stewart hexapod.
-GT40 designed in form of traditional 6DOF table.
In both cases the 6DOF actuator system provides a 4DOF pinion spindle articulation (each axes has about +/- 0.125” displacement range)

GT40, Configuration
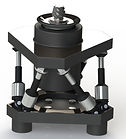
GT41, Pinion Spindle
A unique feature of AGPES is that it could be expanded to build a data base of test results and acceptance criteria leading to the creation of an Expert system that could be used to replace the subjectivity of an evaluation process that currently uses human operators to qualify gear acceptance.
The AGPES has many important technical advantages when compared to other more traditional gear testing systems existing on the market today.
GEl Systems with its experience in the area of multi-DOF system analysis has invested heavily in the development of unique technology to produce a high-performance mechanical system with a state-of-the-art software.
​
The real strength of the GEI’s AGPES design lies in the ability to produce a system level solution. Thus, it is important to understand that system level analysis and perspective is the most effective means of comprehending the trade-offs in this project.
GEl Systems brings to this program experience in Gear related analysis and synthesis as well as experience in closed-loop control and servo hydraulics development.
Transmission Error testing is becoming increasingly important within the vehicle development and production test markets. This is due to -
-
AGMA has developed new standards for gear quality which includes now μrad level for TE. That requires to perform SFT particularly where the gear set is established as a pair right from the beginning of the production cycle.
-
OEM’s are designing and deploying hybrid and electrically powered vehicles. These hybrid and electric power trains generate significantly lower audible noise and reveal previously masked gear noise within the vehicle. This results in the perception of reduced quality and a need to test and refine designs for an overall quieter vehicle.
There is a growing demand in the automotive market (particularly in the research and development environment) for noise reduction produced by a final drive gear set.
This is a critical issue for so called noise sensitive applications such as buses and passenger cars. During the last 10 years the industry has started using requirements for the noise level based on Transmission Error (TE) vs. vibrational information as it has been during the last 4 decades. That requires a new type of SFT testers with enhenced TE measuring capability.
​
Gear manufacturers are seeking the most economically appealing (lowest overall cost and shorter time) methods to produce gears with high performance, lower weight, lower noise and lower sensitivity to the mounting and load conditions to meet necessary functional and performance requirements.
This is important to keep vehicle OEM’s and suppliers economically viable and competitive. It is very common for gear supplier to be awarded with multi -year contract based on supplier’s ability to test gears for TE using advanced SmartSFT.
The following features were described by a number of customers as critical for this type of test:
​
-
The creation of an Expert system that would be used to reÂplace the subjectivity of an evaluation process that currently uses human operators to qualify gear acÂceptance.
-
Simulation of real environmental spatial stiffness;
-
Correlation of gear acceptance with objective functions and gear set specifications and properties.
-
High accuracy & resolution motion control (coarse & fine Settings)
-
Interactive gear analysis software
-
On-Line tooth contact image recognition and force measurement
-
Real time RPC duplication of dynamic service environment
-
DSP for noise analysis and modeling
Based on the main idea of a smartSFT (see the page AboutSFT), the effect of shafts, bearings and supporting structure (housing) deflection can be measured and represented by certain changes in 4 DOF vector with component parameters: E, P, G, Alpha.
The ability to establish a sensitivity matrix for various errors in (mounting conditions) which may take place during assembling the unit inside the housing for all the four DOF to perform a real environmental condition simulation which includes the use of the spatial stiffness of the housing, bearings and shafts in real time. This option is called "dial-in stiffness";
​
The establishment of a tool for an independent & objective acceptance procedure results in creation of the Expert system like EGPES to reduce and then replace operator subjectivity from the process
